Agenda 2025
This year, we are again preparing a programme for you in collaboration with experienced practitioners in the field.
#TAL2025 will present inspiring ideas, practical case studies and space for discussion and your topics.
We will talk about the future of Supply Chain, automation, digitalization, artificial intelligence and other logistics trends.
The Experience Zone will be open throughout the day, where you can meet the conference partners and try out technological gadgets.
The official programme will be followed by a social evening where you could share impressions over good food and drink.
Will you join us?
Tuesday, 20 May 2025
Main Agenda
8:30–9:30 | Registration |
9:30–9:45 |
OpeningRoman Žák, Chairman of the Supervisory Board, Aimtec Richard Brunner, Regional Head of Chamber of Industry and Commerce Regensburg Bernard Bauer, Executive Board Member, DTIHK |
9:50–10:20 |
Automation & AI: The Journey Has Only Just BegunThilo Jörgl, Managing Partner, TEST CAMP INTRALOGISTICS & impact media projects |
10:25–10:55 |
BMW's iFACTORY: Lean – Green – DigitalTobias Mayr, General Manager IT Inbound Logistics, BMW Group |
10:55–11:25 |
Coffee Break |
11:25–11:55 |
AI Transforms Logistics at Škoda AutoMojmír Barák, Logistics Systems Coordinator, Škoda Auto |
12:00–12:40 |
Panel discussion: Digital. Future-Proof?Thilo Jörgl, Managing Partner, TEST CAMP INTRALOGISTICS & impact media projects Tobias Mayr, General Manager IT Inbound Logistics, BMW Group Mojmír Barák, Logistics Systems Coordinator, Škoda Auto Csaba Malatinszki, Supply Chain General Manager, Denso Manufacturing Hungary Pavel Boháč, Chief Executive Officer, Aimtec |
12:40–14:30 |
Lunch and Networking |
14:30–14:55 |
Safran Cabin's Digital TransformationSelim Caluwaerts, Chief Data Officer & DigiMaps Program Director, Safran Cabin |
15:00–15:25 |
6G Networks in the Factories of the FutureJiří Maršík, Group Leader: Measuring and Testing Procesess Development plus Simulation, Bosch Zdeněk Bečvář, Head of 6G Mobile Research Lab, Faculty of Electrical Engineering, Czech Technical University in Prague |
15:30–15:55 |
The Benefits of Standardisation in the Automotive IndustryTomáš Brotz, Automation Engineer for Automotive Standards, Siemens |
15:55–16:20 | Coffee Break
|
16:20–17:00 |
Panel discussion: Trends in Czech logisticsMichal Štěrba, Chief Executive Officer, GZ Media Libor Mihalka, Automation and robotics solutions expert, LogTech Václav Kopecký, Head of Key Accounts ČR, STILL Jan Flodrman, Business Development Manager, Zebra Technologies Rostislav Schwob, Supply Chain Solutions Director, Aimtec |
17:05–17:30 |
Smart Logistics to the Rhythm of MusicMichal Štěrba, Chief Executive Officer, GZ Media |
17:30–17:45 |
Closing |
17:45–22:00 |
Social evening Once the presentations are done, we’ll be moving on to a social evening at Parkhotel Pilsen, with musical accompaniment by Iby Pop. Come after the conference hours for a chat with your colleagues! |
Side section
8:30–17:45 |
#AimtecLab – Aimtec Digital Factory Showcase What does the future hold? Come and try out logistics and manufacturing simulations, practical reporting, our Aimtec SCIx Digital Factory, or AI tools – from chatbots to document data extraction. In AimtecLab, technologies come to life. You can visit AimtecLab in the main hall during any of the breaks in the conference programme. |
Presentations will be interpreted into Czech, German and English. The right to change the conference programme is reserved. |
TAL 2025 speakers
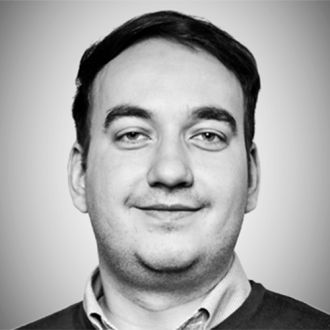
Mojmír Barák
AI Transforms Logistics at Škoda Auto
Mojmír Barák has been part of Škoda Auto’s logistics operations for six years, during which time he has held various positions and contributed to numerous projects within the logistics systems department. He currently leads the Digital Delivery Centre, which focuses on accelerating the digital transformation of logistics processes.
Škoda Auto is one of the most prominent car manufacturers in Central Europe and a member of the Volkswagen Group. The company places long-term emphasis on innovation, efficiency and sustainability across its entire production and logistics chain.
In his presentation, he will introduce not only current and planned initiatives in the field of artificial intelligence, but also the challenges that must be overcome on the path towards an AI-driven future. He will also offer insights into how AI can transform logistics and unlock new opportunities for more efficient and intelligent process management.
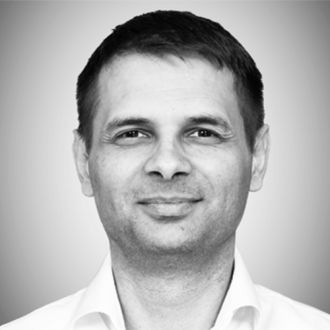
Csaba Malatinszki
Panel Discussion: Digital. Future-Proof?
Csaba Malatinszki has been working at DENSO HUNGARY for 22 years, having started as a Production Planner. Over the years, he has taken on increasing responsibilities and is currently in charge of the entire supply chain, including strategic purchasing, logistics, and warehousing. DENSO HUNGARY specialises in diesel injection systems, emission reduction components, and has recently expanded into the field of electrification.
Throughout his career, Csaba has faced numerous challenges – particularly in situations that required high performance under pressure due to shortages of resources, whether human, financial, or spatial. He believes in the power of the “kaizen mind” (continuous improvement) – a principle he has embraced throughout his career and strives to pass on to his colleagues.
DENSO CORPORATION, a global Tier 1 automotive supplier, produces a wide range of components, including systems for internal combustion engines, thermal management, electrification, and vehicle safety.
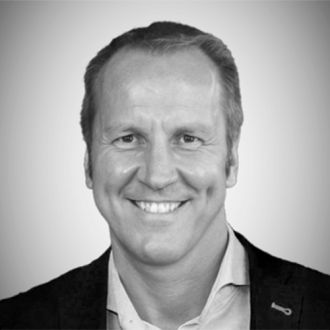
Tobias Mayr
BMW’s iFACTORY. Lean – Green – Digital
After 20 years in various IT roles within the BMW Group – including international assignments at production sites in China, Brazil, the USA, and South Africa – Tobias Mayr now leads the global IT team for inbound logistics across all BMW locations worldwide. His team is responsible for the entire supply chain: from material master data management, material planning, and inventory control to demand and consumption accounting, as well as delivery scheduling, including JIT/JIS processes.
In recent years, his division has developed a comprehensive logistics analytics platform that enables the BMW Group to respond swiftly to volatile conditions. Tobias is passionate about the digitalisation of production and logistics processes, with a strong focus on scalable solutions built on robust platforms. He and his team are currently implementing a global rollout of a standardised logistics template based on SAP S/4HANA across all BMW sites worldwide.
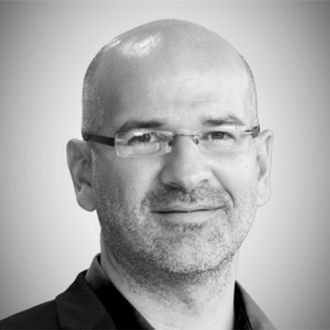
Thilo Jörgl
Automation & AI: The Journey Has Only Just Begun
Thilo Jörgl is a journalist and logistics expert, serving as Managing Partner at impact media projects GmbH in Ismaning near Munich. Since 2018, he has been part of the management team of TEST CAMP INTRALOGISTICS, the IFOY AWARD, and the Logistics Hall of Fame. He also acts as the conference director of ConnectChains – the Humanitarian Supply Chain Conference in Berlin. His areas of focus include supply chain management, automation, software, robotics, and humanitarian logistics.
In his talk, he will explain why the Silicon Economy will dominate this decade in supply chain management, the role AI will play, and which automation technologies are already being applied in companies today. He will also present award-winning solutions from the IFOY AWARD that were tested at the TEST CAMP INTRALOGISTICS in Dortmund.
Thilo will also moderate the panel discussion on the topic: Digital. Future-Proof?
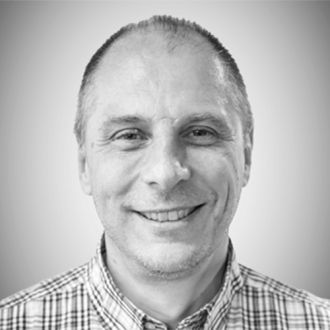
Selim Caluwaerts
Safran Cabin's Digital Transformation
Selim Caluwaerts is an experienced professional in data analytics and information technology, with many years of expertise. He currently serves as Chief Data Officer and DigiMaps Program Director at Safran Cabin, where he is responsible for data strategy and solution implementation. His specialisation lies in leveraging data to optimise processes, enhance efficiency, and drive innovation in the aviation industry. Throughout his career, he has held leadership roles in business intelligence, digital transformation, and data management across various sectors.
Safran Cabin is part of the Safran Group, a global leader in aviation. The company designs and manufactures aircraft interior components and works with major manufacturers such as Airbus and Boeing.
In his presentation, Selim will explore the critical role of data in modern aviation, detailing how Safran Cabin harnesses data-driven insights and applies Machine Learning to enhance operational efficiency, predictive maintenance, and decision-making processes.
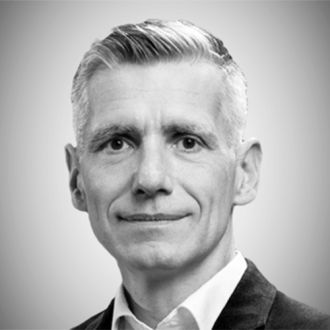
Michal Štěrba
Smart Logistics to the Rhythm of Music
Michal Štěrba joined GZ Media in 2003 after completing his university studies. He gradually rose through the ranks to become Sales Director and has served as CEO and a board member since 2013. GZ Media is the world’s leading producer of vinyl records and a major manufacturer of high-value print products. Headquartered in Loděnice near Beroun, the company also operates sites in Hýskov, Soběslav, and Příbram, with strong expansion into the US and Canadian markets.
GZ Media continuously invests in innovation and automation. The company is now in the second phase of its Smart Logistics project, which is revolutionising the movement of work-in-progress, finished goods, and shipments. In his talk, Michal Štěrba will share how the project was launched, what challenges had to be overcome, and why it makes sense to keep moving forward.
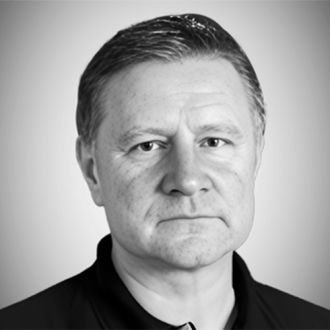
Jiří Maršík
6G Networks in the Factories of the Future
With over 30 years of technical experience, Jiří Maršík began his career focusing on theoretical electrical engineering, followed by microelectronics and wireless networks. He later joined Bosch in České Budějovice, where he now works in the Advanced Technology Development department, responsible for designing and implementing advanced testing and measurement methods.
Currently, he and his team are involved in testing 6G technologies in an industrial environment, in collaboration with Professor Zdeněk Bečvář as part of an ongoing research project. Bosch acts as the industrial partner, providing a real-world testing environment and expert knowledge in collecting, analyzing, and storing product-specific data.
Bosch České Budějovice is a development and production center focused on components for the automotive industry. As one of the largest employers in the region, it plays a key role in research and innovation within the Bosch Group.
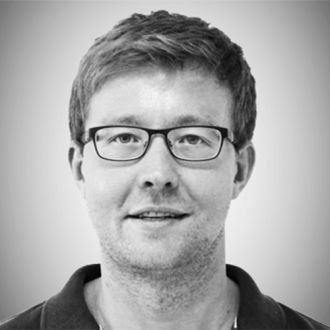
Zdeněk Bečvář
6G Networks in the Factories of the Future
Zdeněk Bečvář is a professor at the Faculty of Electrical Engineering at the Czech Technical University in Prague, focusing on research in mobile communication networks including 4G, 5G, and 6G. He is the author of over 100 scientific publications and co-inventor of four U.S. patents. He leads the 6Gmobile research lab, where he bridges cutting-edge communication technologies with real-world applications in industry, autonomous mobility, and edge computing.
He currently coordinates the international MUSE-COM2 project in collaboration with BOSCH, aiming to develop semantic communication and computation techniques for industrial use. His research has resulted in innovations such as flying base stations, remote robot control via software-defined mobile networks, and autonomous vehicles using edge-based sensor data processing.
Professor Bečvář actively represents the Czech Republic in international research and standardization forums and is a recipient of multiple prestigious awards in wireless communication.
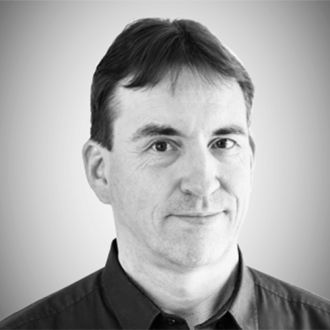
Tomáš Brotz
The Benefits of Standardisation in the Automotive Industry
Tomáš Brotz joined Siemens a year and a half ago as a standardization expert in the field of industrial automation. He began his career as a software engineer focused on industrial applications, data acquisition, and visualization, with experience in networking and databases. He later fully dedicated himself to industrial automation and spent over 20 years delivering projects around the world, particularly for customers in the automotive sector.
In his presentation, he will share the benefits and value of standardization, concrete technical solutions, and real-life implementation experiences.
Siemens Czech Republic is one of the largest technology companies in the country and has been an integral part of Czech industry for 135 years. With more than 7,000 employees, the company provides solutions for industry, distributed energy, public infrastructure, and building technologies. Siemens is also a pioneer in digitalization, automation, and smart infrastructure.
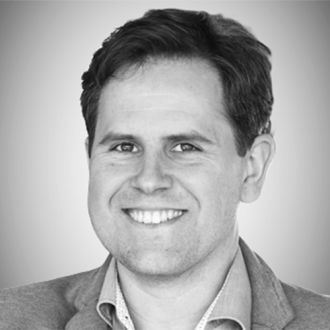
Pavel Boháč
Panel Discussion: Digital. Future-Proof?
Pavel Boháč is the CEO of the consulting and technology company Aimtec, which supports manufacturing and logistics businesses on their journey of digital transformation. He has been with Aimtec since 2013 and led the Advanced Planning and Scheduling (APS) division from 2016. Since July 2024, he has taken on the role of CEO. His vision focuses on strengthening innovation, expanding cooperation with corporate clients, and growing Aimtec’s presence in key international markets — all while preserving the strong company culture that defines Aimtec’s identity.
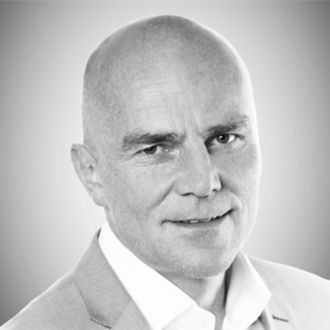
Rostislav Schwob
Panel Discussion: Trends in Czech Logistics
Rostislav works at Aimtec as Supply Chain Solutions Director and is also a member of the company’s Board of Directors. He was one of the key figures behind the development of the Aimtec DCIx system and continues to lead the team responsible for implementing projects focused on the digitalization and automation of logistics and production around the world.
He focuses on emerging trends and actively incorporates them into product modernization to ensure maximum value for customers while aligning with their future direction and development.
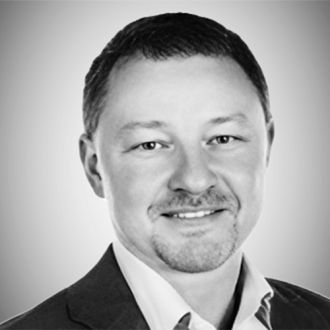
Libor Mihalka
Panel Discussion: Trends in Czech Logistics
Libor Mihalka is the founder of LogTech, a Czech company specializing in automation and system integration of logistics processes. With more than 20 years of experience in logistics and automation, he has contributed to numerous projects involving robotic systems, miniload warehouses, and express delivery solutions. LogTech collaborates with leading technology partners such as Geek+ and Aimtec and actively participates in expert discussions on the future of logistics and automation.
You can look forward to seeing him in the panel discussion at the conference.
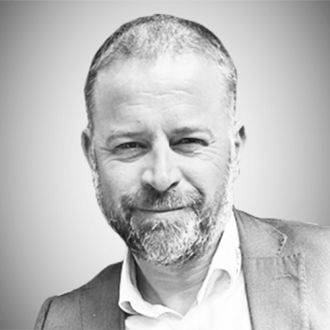
Václav Kopecký
Panel Discussion: Trends in Czech Logistics
At STILL ČR, he leads the Key Account Management team and has over twenty years of experience in the logistics sector. In recent years, he has focused primarily on automation projects implemented across various market segments, in addition to conventional solutions.
At the conference, he will join a panel discussion on trends in Czech logistics, where he will share his experience with automation implementation for customers.

Jan Flodrman
Panel Discussion: Trends in Czech Logistics
Jan Flodrman is a Business Development Manager at Zebra Technologies, focusing on process digitalization in logistics, manufacturing, retail, transportation, and healthcare. He specializes in the implementation of technologies such as RFID, RTLS, machine vision, and automation to improve operational efficiency and accuracy. He actively participates in industry conferences and trade fairs, where he shares his hands-on experience with modern technology applications.
At the conference, he will share his insights during a panel discussion on current logistics trends.